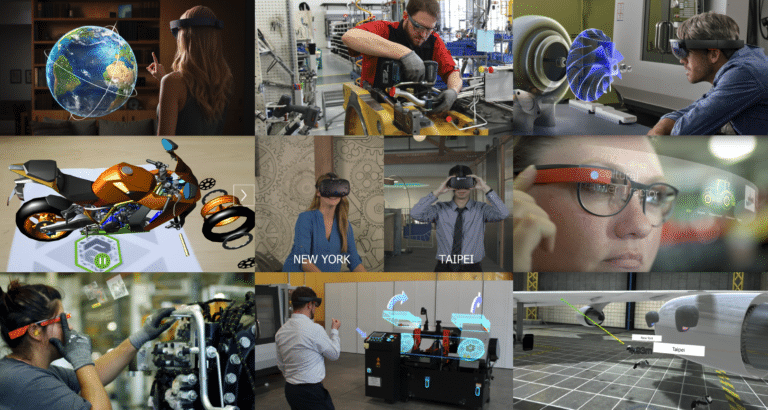
This post is adapted from ARtillry’s latest Intelligence Briefing: Enterprise XR: Impacting the Bottom Line. More can be previewed here and subscribe to access the full report.
There’s been lots of talk of AR’s ability to achieve operational efficiencies. But of course that has to be quantified in a unit of measurement. For most organizations, that unit of measurement is dollars, naturally. But a proxy for dollars can be another quantifiable metric: time.
“There are a couple variables that we typically track, and one is time,” said Upskill CSO Jay Kim at AWE Europe. “It’s simple to measure and the benefit is obvious for time saved in your business process, and what that means as a first-order variable to determine ROI.”
Drilling down to more concrete terms, Kim claims that Upskill sees 30 percent average reduction in project time. And this is a meaningful figure, considering Upskill’s client base that includes GE, Boeing, and Coca-Cola. Compared to other technologies, this is a huge efficiency boost.
“30 percent is a game changing number,” he says. “People in lean manufacturing and continuous improvement will spend millions and millions of dollars chasing a 5 percent improvement… So imagine what you’re able to do when you can go and do things 30 percent faster.”
In addition to time efficiency, another key metric is resolving “exceptions.” These are unforeseen incidents that can slow down production or manufacturing output, such as equipment breakdowns. This hurts in both machine downtime and maintenance costs.
“Each of the trips that they have to go and pay one of their vendors’ technicians to come and repair a piece of bottling equipment is going to cost a minimum of $10,000” said Kim. “So there, the savings are lumpy but each savings makes it a solution that easily pays for itself.”
Google likewise reports that its Glass Enterprise Edition reduces manufacturing time by 25 percent and inspection time by 30 percent. It also reduced doctors’ admin work from 33 percent of their day, to ten percent. And DHL gained a 15 percent boost in supply chain efficiency.
Elsewhere, we see similar time-efficiency gains that align with these figures. Intel recently reported 15 to 45 percent reductions in project time around its warehouse facilities. Though it’s a wide range – representing a variety of job roles – it’s similarly supportive of AR’s real impact.
“We’re running a pilot in our distribution center and putting [AR] on workers who do picking and packing for our parts,” said Intel’s Chris Croteau at an ARiA event. “The first day we had a 15 percent improvement in productivity…The peak that we measured was about 45 percent.”
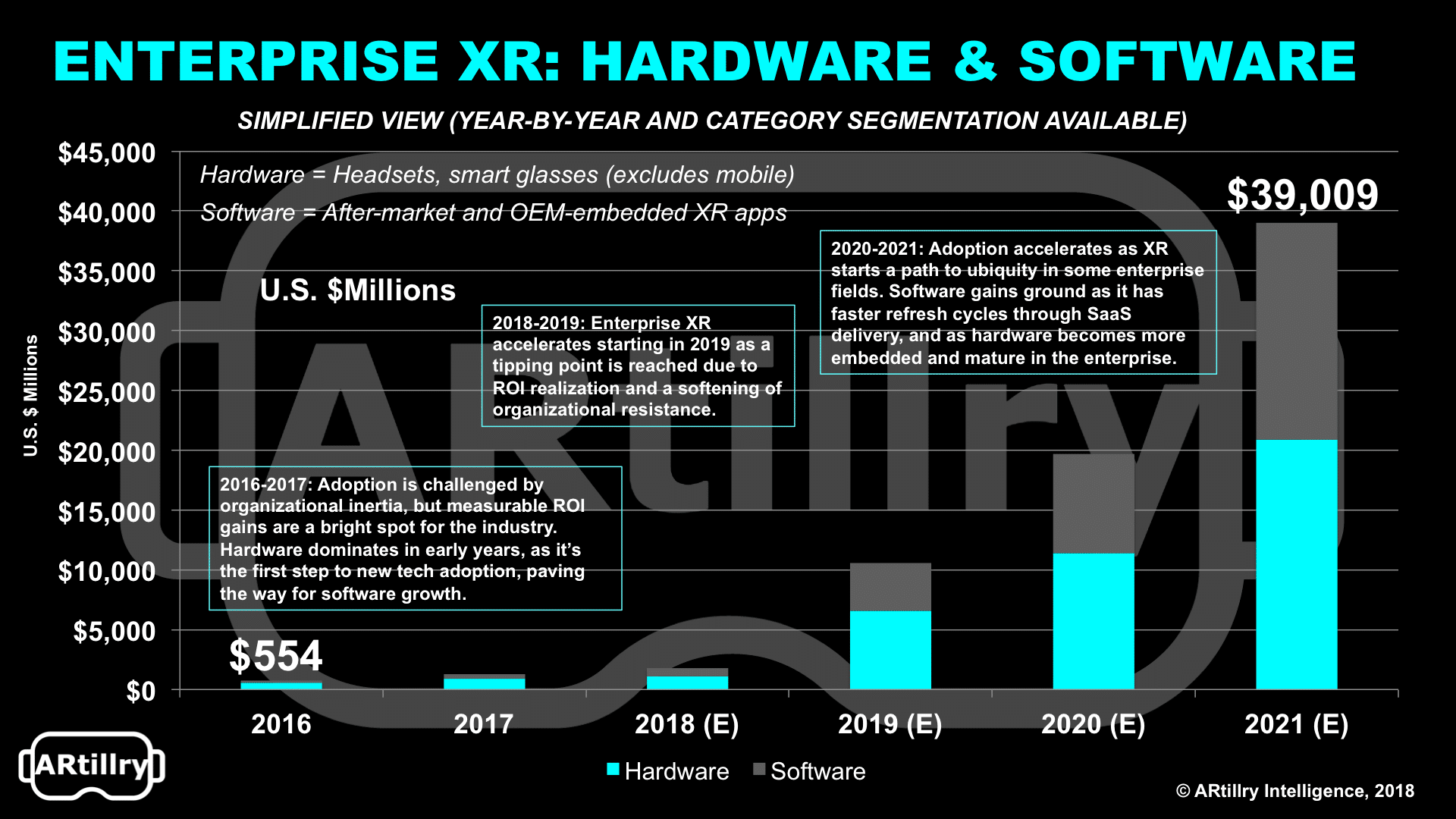
Coca-Cola: A Living Example
Coca-cola is already demonstrating AR’s proof of ROI. It uses AR to fix broken equipment and for “changeovers” to assembly lines. That’s when lines are quickly retooled for different products (e.g. bottle sizes or flavors). It’s all about reducing downtime and increasing the bottom line.
“Whatever you do has to impact the bottom line,” said Coca-Cola Director of Product Management Michael Terrell at AWE Europe. “When a machine goes down, it’s the heartbeat of our operation. So if it’s down, we’re not producing product. Downtime is our enemy.”
To reduce downtime, the company implemented a combination of Google Glass Enterprise Edition and Upskill’s Skylight AR software. One key function is remote assistance for machine maintenance. When a bottle filler recently broke, remote AR-assistance enabled quick recovery.

“One of our techs grabbed the glasses and dialed in a vendor from a few thousand miles away,” said Terrell. “It allowed him to troubleshoot and we got that equipment up and running within an hour. Prior to having this technology, cases like that could end up costing me a whole shift.”
Besides downtime, Terrell underscores hard costs such as travel expenses for flying in a vendor. This can add up to several thousands of dollars per incident. Given the frequency of these unexpected events – not to mention scheduled changeovers – the efficiency gains add up fast.
“When we’re changing over, we’re not producing product.” said Terrell. “From a knowledge transfer standpoint, right there at a touch of the glasses [are] step-by-step directions on changeovers or directions on trouble shooting. So this has really been a game changer for us.”
For a deeper dive on AR & VR insights, see ARtillry’s new intelligence subscription, and sign up for the free ARtillry Weekly newsletter.
Disclosure: ARtillry has no financial stake in the companies mentioned in this post, nor received payment for its production. Disclosure and ethics policy can be seen here.