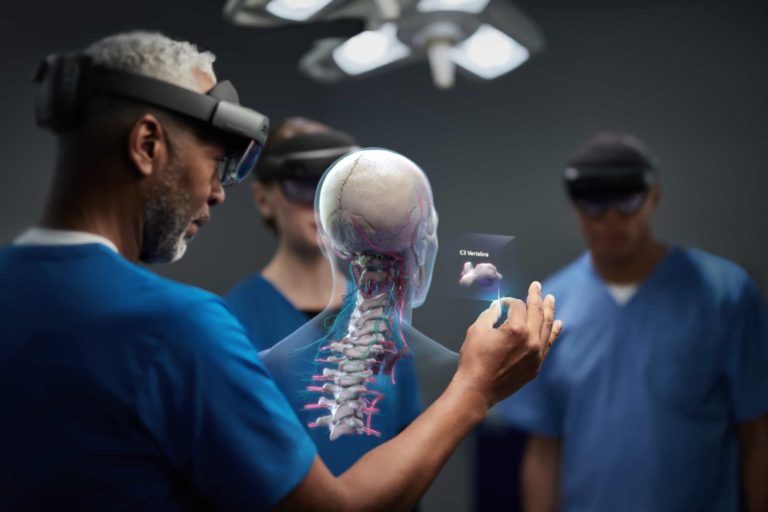
Though we spend ample time examining consumer-based AR endpoints, greater near-term impact is seen today in the enterprise. This takes many forms including camera commerce and collaboration. But the greatest area of enterprise AR impact today is in industrial settings.
This includes AR visualization to support assembly and maintenance. The idea is that AR’s line-of-sight orientation can guide front-line workers. Compared to the “mental mapping” they must do with 2D instructions, line-of-sight support makes them more effective.
This effectiveness results from AR-guided speed, accuracy, and safety. These micro efficiencies add up to worthwhile bottom-line impact when deployed at scale. Macro benefits include lessening job strain and the “skills gap,” which can preserve institutional knowledge.
But how is this materializing today and who’s realizing the above enterprise AR benefits? Our research arm ARtillery Intelligence tackled these questions in its report: Enterprise AR: Best Practices & Case Studies, which we’ve excerpted below, featuring Medtronic’s AR deployment.
Enterprise AR: Best Practices & Case Studies, Volume 1
High-Stakes Outcomes
One area that’s ripe for AR guidance is healthcare. The healthcare vertical is of course expansive and so are the opportunities and points of entry for AR. That can include everything from guiding surgeons through line-of-sight instructions to medical device manufacturing.
These use cases are where Medical device manufacturer Medtronic, with the help of Re’Flekt and Unity, has implemented AR. It allows operators such as surgeons to improve their acclimation to and mastery of medical equipment, which has high-stakes outcomes.
To provide some context, a sizeable challenge for Medtronic is human error due to ineffective training. After spending years in product design, optimization and manufacturing, the “weak link in the chain” can be the human that ends up operating the equipment.
This challenge has gained impact over time as the rate of medical device technology accelerates. That means the cycles of innovation render previous equipment – and the expertise to use it effectively – obsolete at shorter intervals. Training is outpaced by product cycles.
In other cases, it’s the opposite problem: technology deployed in healthcare is outdated and doesn’t integrate with the latest solutions. Lastly, a pain point for Medtronic was the attention and time required by medical records, as they take valuable time away from patient care.
Enterprise AR: Opportune But Underbaked
Brain Encoding
To address the above issues, Medtronic has implemented digital simulators for surgical training in a minimally-invasive way. This involves real patients, but without actual surgery. Instead, Microsoft HoloLens guides surgeons while they’re using the equipment.
The company reports that surgeons who practice in the simulation show an error rate of 15 percent in real surgery, compared to an 82 percent error rate for those who didn’t train in the simulator. This success rate results from the effective brain encoding that AR can instill.
Another area that AR adds value is further upstream: manufacturing. Medtronic has implemented AR at that stage, including production. Here the complex process of assembly line “changeovers” (modifying equipment for a different product output) can benefit from AR.
“In manufacturing, we have various stages of manual, semi-automatic, and automatic processes,” Medtronic’s technical fellow William Harding told Re’Flekt. “Those processes must be transferred across many facilities where there is a lack of standardization around the data. If I add a new process to a production line, many questions need to be addressed: How do I get the process to integrate seamlessly? How do I accomplish that without using paper-based systems? The goal is to speed up efficiencies and reduce scrap while also reducing human error. When we create a new process in lean manufacturing, we need to establish the most ergonomic way for an operator to perform their tasks within a sterile environment. We also want them to complete these tasks in the most efficient way possible, while delivering a high-quality product. There are many factors to be considered.”
Similarly, Medtronic has begun to use AR simulations to train assembly workers versus cardboard models. Similar to surgeons’ error reduction, manufacturing front-line workers can use AR in simulated environments to save money. That happens to the tune of $30,000 per training.
“It used to take us two and a half weeks to build a cardboard set-up with five process stations,” said Harding. “For one training session, we also needed at least eight to ten people off the production floor, who then weren’t engaged in manufacturing products while they were in training. It would cost us about $30,000 for one training effort with the cardboard set-up. We usually require five sessions in total to get everything right, and by the time we decide that everything is ready, we’re making changes five minutes later. In contrast, creating AR content to train my colleagues took me less than two hours. They can access it individually whenever required (including in the manufacturing floor cleanroom environment), and we can easily adapt it if changes occur in the set-up.”
Headworn AR Revenue Forecast, 2019-2024
Field of View
Speaking of saving time, doctors and nurses often get diverted from patient care due to the processing of medical records, as noted earlier. Here too, AR has come to the rescue by streamlining the transfer of records to a doctor’s field of view where it’s needed.
“EMRs (Electronic Medical Records) and EHRs (Electronic Healthcare Records) were built to improve billing,” said Harding. “Any attempt to digitize these records and integrate the information with other solutions was simply a digital version of the paper-based format. This makes the management of medical records for medical staff very time consuming as they transcribed the manually collected data or transferred the data between dissimilar systems. I found that doctors spend around 52 percent and nurses around 47 percent of their time transcribing health-related data from one system to another, which uses valuable time and skills that they could be investing in the patient. To truly connect devices and digitize our data, we need a transformative approach. That’s what XR technology offers.”
This invokes an important lesson that continues to emerge throughout our case studies. A key success factor in enterprise AR deployments is to create benefits that are felt by the front-line professionals who are proposed to use it. Their buy-in is instrumental in effective deployments.
For example, the medical professional time-saving benefits outlined above not only help Medtronic and medical institutions, but they have tangible quality of work-life advantages for doctors and nurses. This should be a key lesson for AR’s success and its enterprise rollouts.
“There’s no better way to prove that your solution provides value than if the users change their habits and use your tool instead of what they had before,” Re’Flekt CMO and president Dirk Schart told ARtillery Intelligence. “The clearest path to success is to have clear goals, business-side buy-in, and most importantly to prove value to end-users.”
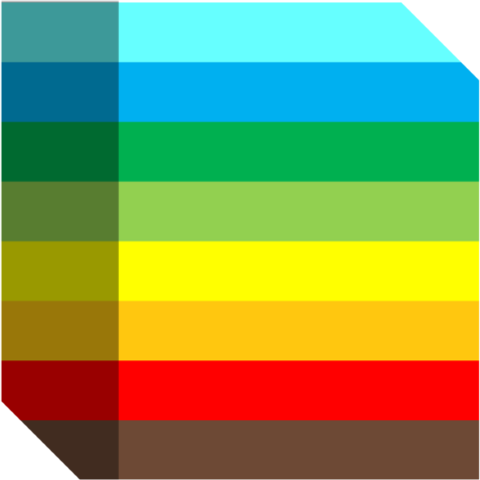