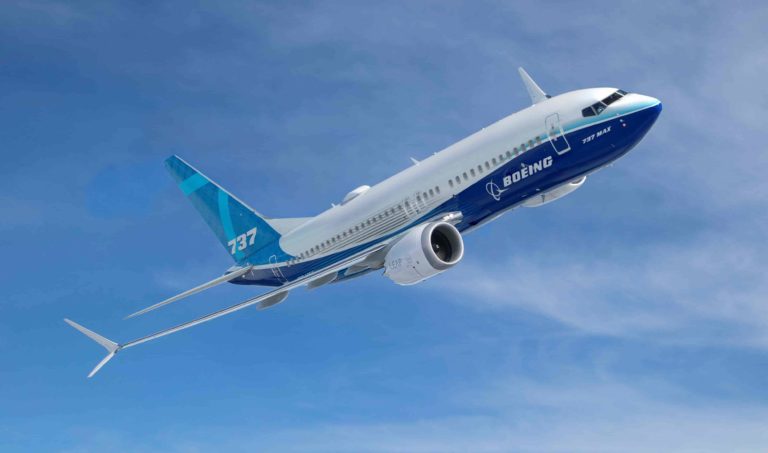
Though we spend ample time examining consumer-based AR endpoints, greater near-term impact is seen in the enterprise. This takes many forms including brands that use AR to promote products in greater dimension, and industrial enterprises that streamline operations.
These industrial endpoints include visual support in areas like assembly and maintenance. The idea is that AR’s line-of-sight orientation can guide front-line workers. Compared to the “mental mapping” they must do with 2D instructions, visual support makes them more effective.
This effectiveness results from AR-guided speed, accuracy, and safety. These micro efficiencies add up to worthwhile bottom-line impact when deployed at scale. Macro benefits include lessening job strain and closing the “skills gap,” which can preserve institutional knowledge.
But how is this materializing today and who’s realizing enterprise AR benefits? Our research arm ARtillery Intelligence tackled these questions in its report: Enterprise AR: Best Practices & Case Studies, Vol 2. We’ve excerpted it below, featuring Boeing’s AR deployment.
Enterprise AR: Best Practices & Case Studies, Volume 2
High Stakes
Before going into the details and dynamics of what Boeing has accomplished with AR, it’s worth noting that this follows an earlier case study we did on the company. In that previous work, Boeing used AR to guide its technicians to assemble the wire harnesses of its aircrafts.
Specifically, AR systems using Google Glass Enterprise Edition helped technicians affix wires in the right places. This replaced stacks of 2D paper manuals and helped them perform quality checks and summon remote support for additional validation in a hands-free way.
Not only is this process visually complex – thus enhanced through line-of-sight support – but the stakes are high. It’s critical that passenger aircraft wiring is done in a safe and standards-compliant way. Lessened cognitive load for technicians helps boost quality and accuracy.
That brings us to the present. Revisiting Boeing’s AR-assisted assembly for this report, the company has doubled down on AR. That includes the AR hardware it’s using, the functional areas to which it’s applied, and where it’s going next. AR is evolving and Boeing is evolving with it.
First, it upgraded its hardware to Microsoft Hololens 2 which means greater positional accuracy. It also expanded AR-guided functions beyond wire assembly to equipment-rack installation and inspecting automated drilling procedures. AR is now deployed at 15 global facilities.
Case Study: Boeing Cuts Production Time with AR
Elusive & Challenging
And the results? Boeing has achieved 88 percent first-pass accuracy. This is the rate that the first assembly is done accurately – an elusive and challenging figure to perfect. Because first-time rates aren’t 100 percent, subsequent passes are traditionally required.
Greater first-time accuracy means operations are not only more accurate but cost-efficient, due to less follow-on work. AR also helped Boeing reduce task time by 20 percent. And all the above has positioned Boeing to master its next project: Air Force One (speaking of high stakes).
Indeed, a regular 747 has 150 miles of wiring, but the highly-modified Air Force One has about 5x that. So AR will play a key role in assuring the safety of the next addition to the Presidential fleet. This will include 20 HoloLens 2 units for 80 technicians – a big jump in its AR scale.
Lastly, a key lesson is how Boeing was able to deploy AR systems without the adoption friction that’s endemic to enterprise AR. VP for Materials and Manufacturing Research, Laura Bogusch attributes this to effectively showing technicians that AR can reduce job strain.
“Folks are really excited when you can demonstrate that it’s making their job easier,” she said at AWE USA.
We’ll pause there and circle back in the next report excerpt with another enterprise AR case study. Meanwhile, read the full report here and see our video takeaways below…
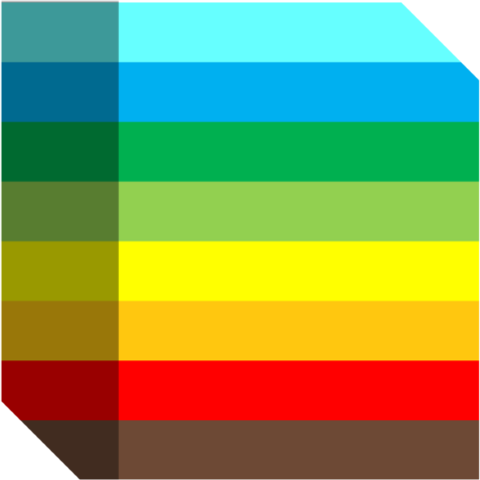