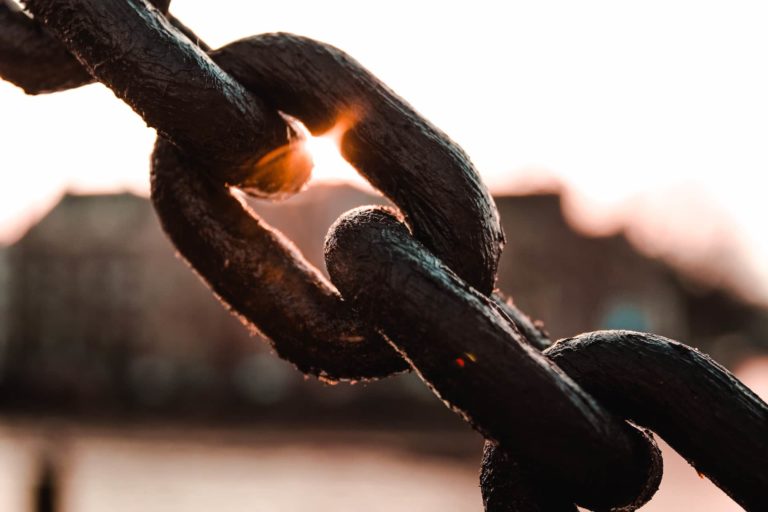
Many supply chains can’t withstand unplanned delays, disruptions, and downtime — the ripple effects extend from production to delivery. Can AR increase their resiliency?
How AR Is Changing Supply Chain Management
While logistics companies are swiftly modernizing, they’re still prone to the effects of inclement weather, equipment breakdowns, and labor shortages. Globally, there were over 11,640 supply chain disruptions in 2021, a massive increase from the 6,192 disruptions in 2020.
Some business leaders have turned to AR for supply chain management to improve their resiliency to disruptions and delays. AR enhances operational visibility since it leverages real-time data streams to enable monitoring and visualization.
AR also improves supply chain management’s accuracy by displaying up-to-date visuals to decision-makers as the need arises, whether they’re walking around the warehouse or sitting in their offices. Since headsets display key points as summarized, interactive graphics, they learn of delays, updated metrics and relevant trends as soon as possible.
When business leaders have a constant stream of data in front of them, they can more easily coordinate with their vendors and partners. Having an unintrusive overview of messages and critical details can help them improve collaboration and enhance efficiency.
Given that a communication breakdown is a common issue for many logistics companies, many decision-makers would be more than happy to adopt AR tech. This kind of interest drives adoption in the logistics sector, reshaping supply chain management.
AR Applications in Every Stage of the Supply Chain
Suppliers would benefit from leveraging AR for quality control. Since this stage is vital — the rest of the supply chain doesn’t exist without it — improving its defect detection rate could lead to fewer downstream delays.
In manufacturing, one hour of unplanned downtime cost 50% more in 2021-2022 than it did in 2019-2020. Naturally, guided maintenance and employee training are some of the best AR applications since they reduce human error, workplace accidents and equipment breakdowns, resulting in more uptime.
Warehousing AR tech could improve inventory management by providing visual shipment overviews, helping workers know when to move, order or transfer stock. AR applications like this aren’t hypothetical — John Rainey, the chief financial officer of a very well-known multinational retail giant, said it increased employee efficiency significantly at his company.
Distributors and delivery drivers could use AR for inventory tracking, route optimization or address location. Doing so would improve customer satisfaction rates, cut refueling costs and strengthen coordination.
Even the reverse supply chain — where products move from customers to suppliers — can benefit from implementing AR tech. Consumers can use it to view clothes, furniture, cosmetics and decor before they buy, reducing the number of returns.
AR Technologies Can Be the Catalyst for a Positive ROI
Virtual overlays for warehouse logistics let decision-makers view key performance indicators, notifications, and critical data points in real time. Since AR is dynamic and continuously changes with the user’s surroundings, it enhances efficiency.
AR for assembly line quality control during production could lead to a substantial positive return on investment (ROI). Research suggests workers who wear AR headsets complete inspections substantially faster and make fewer mistakes, resulting in fewer downstream delays.
AR tech for decentralized employee education can increase ROI at every stage of the supply chain. Companies can save time and money by providing interactive sessions and real-time guidance for staff. It would simplify on-the-job training since headsets don’t obstruct views, are lightweight and can’t induce virtual reality (VR) sickness.
Considering small businesses spent 59 hours on training per employee in 2023, being able to complete training faster — and with fewer mistakes — than traditional techniques is ideal. This way, they can significantly save on labor. AR applications like these contribute to a resilient supply chain.
Another way this tech can catalyze a positive ROI is through the value it generates as an investment. According to some estimates, the AR and VR market will reach $294 billion in 2024, a tenfold increase from its $30.7 billion valuation in 2021. Adoption could grant logistics companies a competitive edge.
Implementation Challenges to Consider
While hearing about all of these benefits may convince someone AR is the right solution for their pain points, they shouldn’t rush adoption. After all, effective implementation takes time. A lack of infrastructure is one of the biggest challenges to consider. If they don’t have the tech, talent, and data, they won’t be able to generate insights.
Knowledgeable employees are fundamental since many supply chain AR applications rely on them. Whether employers want to improve their assembly lines, transportation routes, or maintenance programs, their workers need to be on board with — and understand how to work — the new tech.
Even then, dirty data could pose an issue. If they don’t check dates, remove duplicates, fix outliers, and fill in missing values, their insights will be skewed or irrelevant. Sources are another big consideration — data scientists should adequately vet them before aggregating information. Clean and reliable data is fundamental to any AR application.
AR’s Place in Supply Chain Management
AR isn’t new tech, but it’s taken time to reach production and distribution. Now that it’s here, companies can use it to make their supply chains more resilient, improving their ROI and minimizing unplanned downtime.
Devin Partida is Editor-in-Chief at ReHack Magazine and editorial contributor at AR Insider. See her work here and follow her @rehackmagazine.
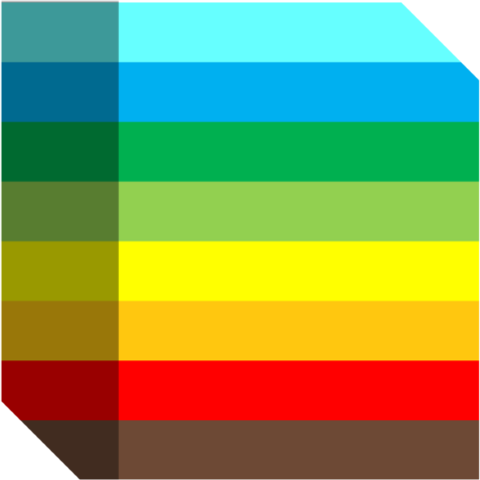