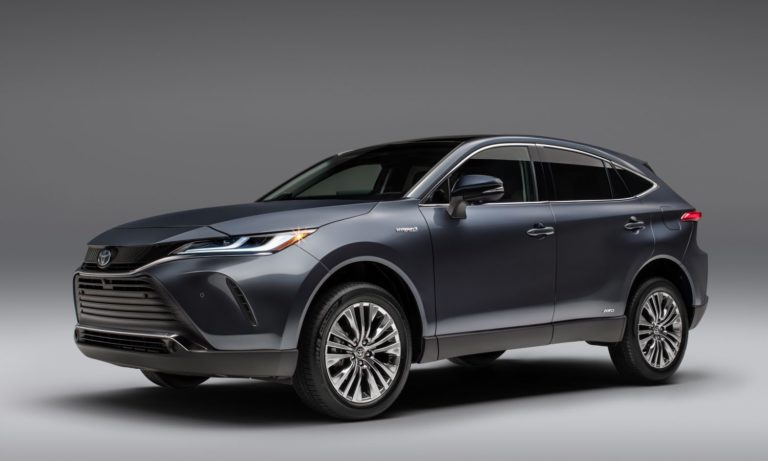
Though we spend ample time examining consumer-based XR endpoints, greater near-term impact is seen in the enterprise. This includes brands that use AR to promote products in greater dimension (B2B2C) and industrial enterprises that streamline their own operations (B2B).
These industrial endpoints include visual support in areas like assembly and maintenance. The idea is that AR’s line-of-sight orientation can guide front-line workers. Compared to the “mental mapping” they must do with 2D instructions, visual support makes them more effective.
And with VR, employee training and onboarding can be elevated through immersive sequences that boost experiential learning and memory recall. It also scales given that far-flung employees can get the same quality training, versus costly travel for senior training staff.
Altogether, there are micro and macro benefits to enterprise XR. The above micro efficiencies add up to worthwhile bottom-line impact when deployed at scale. Macro benefits include lessening job strain and closing the “skills gap,” which can preserve institutional knowledge.
But how is this materializing today and who’s realizing enterprise XR benefits? Our research arm ARtillery Intelligence tackled these questions in a recent report. It joins our report excerpt series, with the latest below on Toyota’s application of AR for guided maintenance and training.
Scale & Standards
As one of the world’s largest auto manufacturers, Toyota’s operations occur on a massive scale. That means any gains (or losses) in operational efficiencies can have outsized impact when implemented widely. In that spirit, one of Toyota’s most important internal metrics is speed.
That applies to several areas of its operations but is most impactful in auto assembly. The faster it can assemble cars (while maintaining quality standards of course), the faster it can bring products to market. This need for speed applies to other parts of the value chain, such as training.
To reach the above goals, Toyota adopted Microsoft HoloLens 2 and Remote Assist for “see what I see” support for front-line workers via live 2-way video and annotations. This upskills and empowers front-line workers, while making scarce senior expert talent cover more ground.
Beyond live remote support, 365 Guides provides holographic line-of-site guidance through pre-authored sequences. Microsoft also worked with Toyota to ensure reliable positional tracking by establishing anchor points on car models to lock 365 Guides sequences in place.
So what were the results? Since implementing HoloLens 2 along with Remote Assist, 365 Guides, and Azure Spatial Anchors, Toyota reduced training time by 50 percent. This resulted from both factors noted above: upskilling novice workers and making senior experts more scalable.
Lessons & Takeaways
So what did we learn? One takeaway from Toyota’s AR implementation is that AR guidance can work on many levels. Remote Assist not only empowers front-line workers with live support, but can record sessions, thus elevating institutional knowledge with on-demand training materials.
For example, content can then flow into 365 Guides to create indexed AR sequences to be consumed on demand. Additionally, Toyota is an exemplar in acknowledging the need for IT department buy-in – a key factor that we examined in a recent installment of this series.
By utilizing Microsoft software and hardware, IT scrutiny was reduced because they viewed the technology as any Windows laptop. This is a key consideration, given that AR adoption and implementation have enough headwinds on their own, without raising IT concerns.
The bottom line: thoughtfully eliminating points of organizational resistance is critical in enterprise XR. We should also say in fairness that, though the lessons above sustain, Microsoft has retreated from the enterprise AR market to some degree, given HoloLens’ recent discontinuation.
We’ll pause there and pick it up in the next installment with more challenges facing Enterprise XR, and how some adopters are getting over the hump…
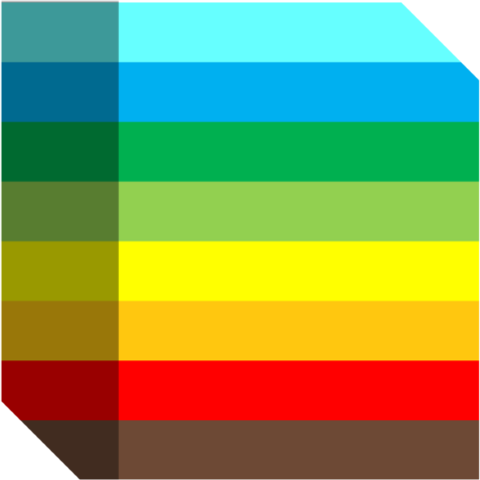