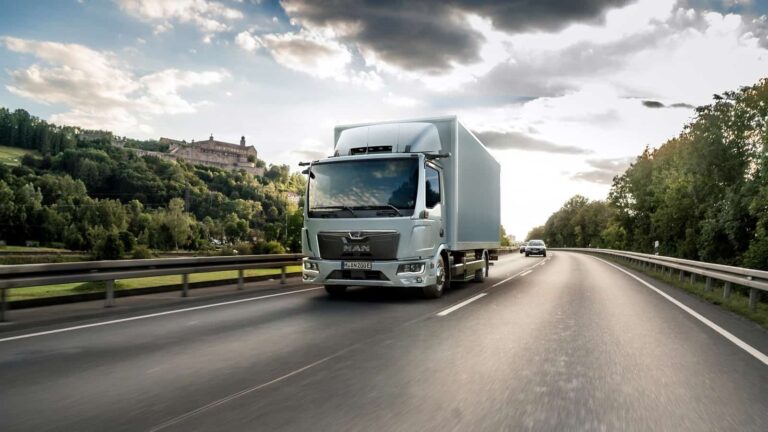
Though we spend ample time examining consumer-based XR endpoints, greater near-term impact is seen in the enterprise. This includes brands that use AR to promote products in greater dimension (B2B2C) and industrial enterprises that streamline their own operations (B2B).
These industrial endpoints include visual support in areas like assembly and maintenance. The idea is that AR’s line-of-sight orientation can guide front-line workers. Compared to the “mental mapping” they must do with 2D instructions, visual support makes them more effective.
And with VR, employee training and onboarding can be elevated through immersive sequences that boost experiential learning and memory recall. It also scales, given that far-flung employees can get the same quality training, versus costly travel for senior training staff.
Altogether, there are micro and macro benefits to enterprise XR. The above micro efficiencies add up to worthwhile bottom-line impact when deployed at scale. Macro benefits include lessening job strain and closing the “skills gap,” which can preserve institutional knowledge.
But how is this materializing today, and who’s realizing enterprise XR benefits? Our research arm ARtillery Intelligence tackled these questions in a recent report. It joins our report excerpt series, with the latest below on MHS work to AR-enable its equipment maintenance operations.
Smarter Systems
MHS has a commercial vehicle service network to service MAN commercial vehicles across Romania. This network consists of 150 technicians, but only 8-10 senior experts. Romania mandates technician training twice per year, which requires experts to travel to train them.
Beyond training, senior experts have to assist field technicians on demand as incidents occur, such as expert diagnosis. All the above is not only sub-optimal from a resource-deployment and scalability perspective, but leads to burnout and early retirement for senior experts.
Travel requirements also cause costly downtime for the client’s vehicles. All of these issues culminated and led MHS to develop smarter systems. It started with the construction of a centralized video conferencing facility to solve training, maintenance, and diagnostic challenges.
Here, experts can place-shift their valuable knowledge in operationally efficient ways. They accomplished this through Cisco Webex Expert on Demand software, running on RealWear’s HMT-1. Field technicians patch in experts whenever they encounter diagnostic challenges.
RealWear’s see what I see capabilities include HD video and photos, as well as directional annotations so that remote experts can assist field agents spatially. This is necessary for complex diagnostics, compared with “flying blind” with voice-only communication.
Lesson in Scalability
So what were the results? Diagnosis time of vehicle repairs was reduced by 75 percent, and travel was reduced by 50 percent. There were also tangible travel cost savings given the place-shifting benefits of remote support noted above. Savings include 2,700 liters of fuel per month.
As for strategic takeaways, this case study is a lesson in scalability. MHS was challenged in scaling its high-value senior experts. By having to physically travel to resolve issues – requiring up to 12 hours of ground transportation – there was a bottleneck in their deployment.
AR eliminated that bottleneck by allowing a scarce resource to placeshift itself from a centralized location, thus covering more ground. This was enabled functionally by the ability to substitute in-person interaction through see-what-I-see support using RealWear headsets.
Other factors were required in terms of tech specs, including HMT-1’s ruggedized body and voice-optimized Android apps with noise cancellation. This enabled effective communications in noisy industrial environments – a key consideration in any industrial AR deployments.
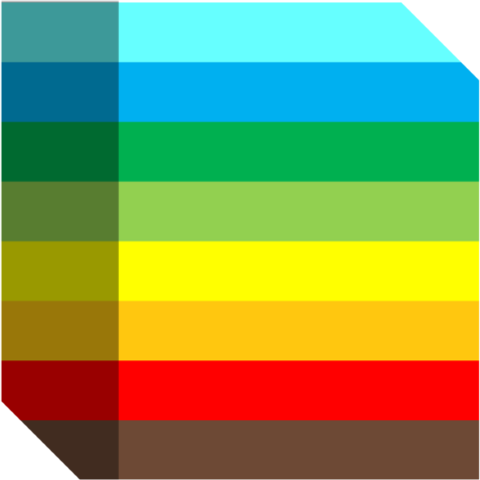