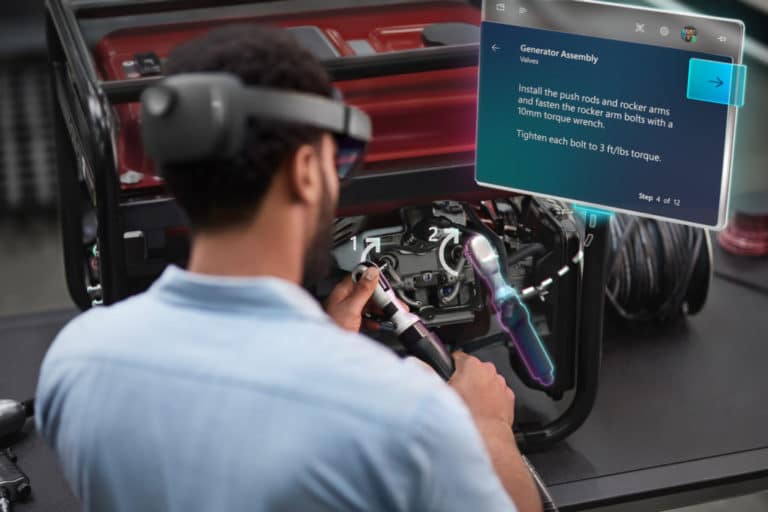
This article was contributed by Scope AR CEO Scott Montgomerie. It is part of AR Insider’s editorial contributor program. Find out more or contact us to participate here. Authors’ opinions are their own.
Automation will create problems in the enterprise — AR can solve them
by Scott Montgomerie
There’s no question that automation and artificial intelligence will profoundly reshape how work will get done. They could be as transformational as the IT era was to enterprise business just a generation ago. But how many jobs will be erased in the process? When a company unleashes AI, does it help or hurt its workforce?
I predict that enterprise companies will always need humans. They’ll always need to optimize productivity, improve job satisfaction, close skills gaps and shrink downtime. And today — not years from now — augmented reality platforms can uniquely solve problems where automation and the workforce intersect. Augmented reality can help retain, and even create jobs, that automation can never fill. By providing contextually aware information in a convenient and consumable format, workers now have the ability to pair innately human characteristics, such as critical thinking skills, with knowledge-on-demand to train and gain skill sets on the fly, with little to no previous experience.
Fact or fiction: the robots are coming for your job
By now, the fearful reports are familiar: AI will swallow entire categories of careers, from factory jobs to truck driving to customer service and middle-manager roles. So will AI really kill 20 million manufacturing jobs in the next decade, as Oxford Economics predicts?
I see widespread workforce augmentation as a far more likely outcome than wholesale workforce automation. It’s highly possible that AI can create more jobs than some people worry that it might eliminate. And there’s evidence: according to a report commissioned by ZipRecruiter, in 2018 alone, AI created three times more jobs than it destroyed.
Amazon — no stranger to automation and robot-assisted warehouse facilities — recently made global headlines when they announced a $700 million investment to re-train a third of its workforce with technical skills like coding. It’s a massive initiative that underscores how deeply committed they are to automation technologies, they’re also recognizing they’ll need a highly-skilled workforce to run them. Yes, there will be more robots at Amazon, not fewer. But the company is aiming to address skills gaps that will only widen in coming years. And it’s doing so by investing in 100,000 people, not just automation technologies.
This approach to automation is smart, for two reasons. For many employers, there are two key challenges to managing workforce costs: 1) training, ensuring your people have access to critical knowledge that is easy to find and consume in real-time and 2) retention of the workers you’ve already invested in. Replacing a highly-skilled worker can cost 400 percent of their annual salary, according to one estimate.
Your workforce is already changing
Transformational technologies like AI are advancing quickly, and more companies are finding ways to deploy them as they evolve. As businesses look to AI to reshape their workforce, it’s important to remember that the workforce is already changing, in very human ways.
At many U.S. companies, older employees are aging out of the workforce. According to the Wall Street Journal, the labor force is growing far more slowly than it did in decades prior. Overall productivity has also declined. And, older workers are staying in their jobs for years longer. Massive workforce re-skilling is an option, but it has a very real cost. (Just ask Amazon.)
However, losing a highly-skilled subject matter expert (SME) also carries a critical cost. Unilever, an enterprise customer of ours, told us that in the next five years, they’ll lose 330 years of experience to retirement — in a single facility alone. When an SME retires, your business shouldn’t lose a career’s worth of institutional knowledge. Augmented reality offers businesses an easy way to transfer this knowledge that new-hires need to be successful and retain it long-term to help build the next-generation of a skilled workforce.
Augmentation vs. automation: Why AR is the answer?
In industries like manufacturing, uptime is everything. When something goes wrong, it can adversely impact processes down the line. Faults and failures need to be monitored and corrected as quickly as possible. Human error is the source of nearly a quarter of all unplanned downtime in manufacturing, which cost trillions in losses to businesses each year. How can human error be minimized? AI is a long way off from identifying equipment failures and then automatically fixing them.
Augmented reality, at its core, is a new user interface — a way for humans to visualize and interact with data in more intuitive ways than before. Humans evolved to interact with the world with their hands and their eyes — interacting with 2D data like words and spreadsheets is merely an inaccurate abstraction, and underutilizes one of the most powerful parts of the brain – the visual cortex. The visual cortex enables a person to consume, filter and process vast amounts of information about the real-world, and utilizing this power to interface with the power of computers is an amazing opportunity. In this way, we can augment humanity by merging the best of both worlds; we can leverage the near-infinite and perfect memory capacity of networked computing power, along with the vast processing power of those computer systems, with the intelligent reasoning and extreme adaptability of the human mind and body.
Using this mix, we can leverage the strengths of both while overcoming the weaknesses of both. AI is far from generalized intelligence (although OpenAI is trying), and robots are far from perfect in actuating and interacting with the world. Augmenting humans with contextually relevant data and insights (potentially from IoT and AI systems) can be an extremely beneficial pairing.
In an enterprise context, AR can help workers alleviate downtime and more accurately assemble, repair or conduct maintenance on complex machinery. AR-assisted workers in manufacturing or field service can access contextual digital overlays and step-by-step instructions. They can access previously recorded support sessions, complete with AR annotations, to see how others solved a problem or completed a task on the exact same piece of equipment on which they’re working. And workers can even initiate a live, AR-enabled video session with a remote expert who can see what they see, and talk them through a task, dropping in pre-built AR instructions or drawing on the worker’s real world view to help along the way. It’s expert knowledge, on-demand, shareable across the enterprise and accessible exactly when it’s needed.
While some worry about the impending automation apocalypse as the ultimate job eliminator, AR can create opportunities to build a smarter workforce that will exist alongside automation tools like robots and AI. It’s an ideal platform for transferring and retaining expertise from experts to those learning new skills, regardless of physical location. It can also be used to bridge your company’s data and your employees in the real world, boosting productivity and minimizing costly downtime. And, when workers are more productive and better at their jobs, overall job satisfaction improves, and that’s a win for everyone involved.
Scott Montgomerie is CEO of Scope AR. Since co-founding the company in 2011, Montgomerie was one of the first executives to get augmented reality (AR) tools in use by multi-billion dollar corporations
A version of this article previously appeared in VentureBeat, and has been repurposed here with the author’s permission.
For deeper XR data and intelligence, join ARtillery PRO and subscribe to the free AR Insider Weekly newsletter.
Disclosure: AR Insider has no financial stake in the companies mentioned in this post, nor received payment for its production. Disclosure and ethics policy can be seen here.