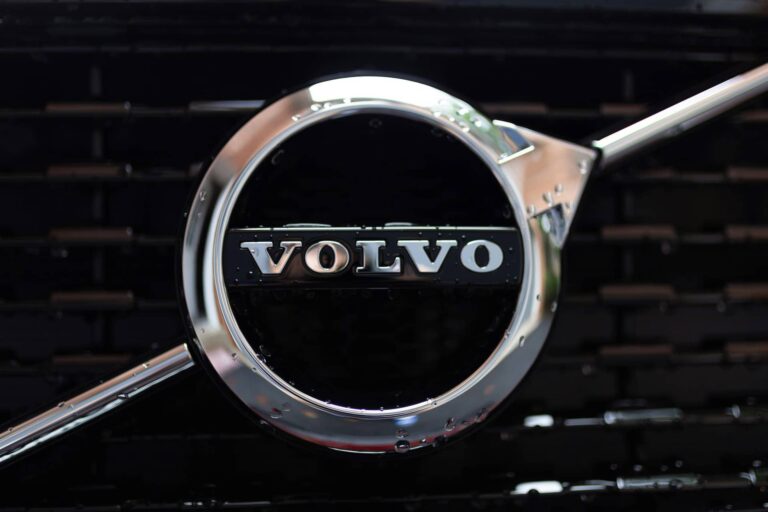
Though we spend ample time examining consumer-based XR endpoints, greater near-term impact is seen in the enterprise. This includes brands that use AR to promote products in greater dimension (B2B2C) and industrial enterprises that streamline their own operations (B2B).
These industrial endpoints include visual support in areas like assembly and maintenance. The idea is that AR’s line-of-sight orientation can guide front-line workers. Compared to the “mental mapping” they must do with 2D instructions, visual support makes them more effective.
And with VR, employee training and onboarding can be elevated through immersive sequences that boost experiential learning and memory recall. It also scales given that far-flung employees can get the same quality training, versus costly travel for senior training staff.
Altogether, there are micro and macro benefits to enterprise XR. The above micro efficiencies add up to worthwhile bottom-line impact when deployed at scale. Macro benefits include lessening job strain and closing the “skills gap,” which can preserve institutional knowledge.
But how is this materializing today and who’s realizing enterprise XR benefits? Our research arm ARtillery Intelligence tackled these questions in a recent report. It joins our report excerpt series, with the latest below on Volvo’s activations with AR-guided quality assurance work.
Digital Threads
Volvo Group manufactures trucks, buses, and industrial engines. Its engines contain 13,000 variants which introduce complexity and the need for quality assurance (QA). Each engine requires 40 checks, with 200 possible QA variants that must be completed in 8 minutes.
Training new operators takes about five weeks, and the QA procedures themselves are paper-based, which creates extraneous administrative costs and cognitive load for operators. It also misses an opportunity for “digital threads” and intelligent lifecycle management.
To evolve these processes, Volvo implemented PTC Vuforia for AR-guided instruction in the QA process, and to capture digital threads for lifecycle management by recording session data. It also utilized PTC’s Thingworx IoT platform to integrate data from disparate systems.
That last part is critical, drawing on CAD files, engineering updates, and product lifecycle management. This is where PTC shines given its strength in not only AR but several other enterprise software systems. AR works best when it integrates with such systems.
For Volvo, this all translated to delivering intelligence to the places it’s needed most – decision points for machine inspection. And through AR, this intelligence was visually anchored on relevant machine parts, including step-by-step instructions and real-time operational insights.
Bi-Directional Flow
And the results? Volvo Group reduced the QA process for new engine integrations from more than a day to less than an hour – a 90 percent reduction in total. It also achieved a 60 percent reduction in training time. All of this resulted in $1000+ savings, per QA station, per year.
As for strategic takeaways that can be extracted, it’s all about optimizing systems using data insights. In addition to removing the cost and risk of paper-based approaches, Volvo’s Group’s AR-based system empowered QA technicians to capture engineering defects and other issues.
These findings could then be transmitted upstream to improve engineering and manufacturing processes. This bi-directional data flow created an effective QA feedback loop. Furthermore, Volvo Group’s work demonstrates how AR and IoT go together, as noted above.
Put another way, AR serves as the interface for IoT data, while IoT provides the intelligence backbone for AR systems. The whole is greater than the sum of its parts as Volvo Group has shown by using PTC Vuforia and Thingworx in tandem. This is where AR can best hit its target.
Header image credit: Adam Cai on Unsplash
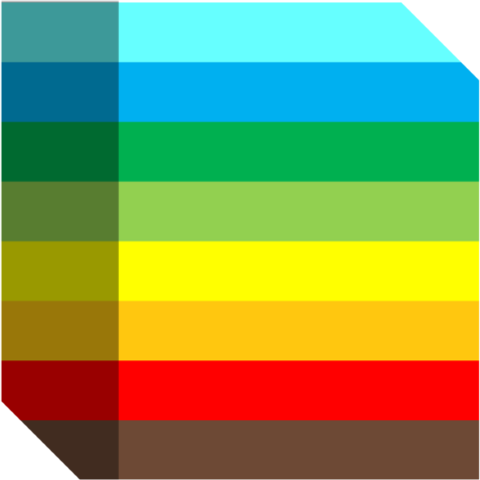