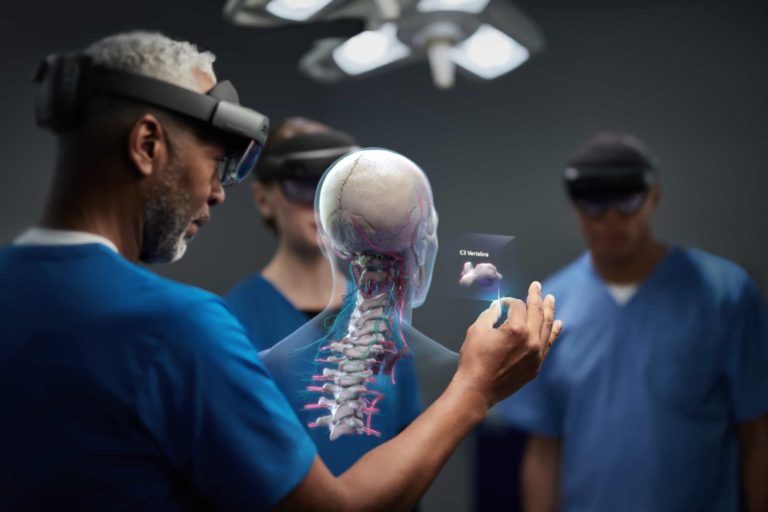
Though we spend ample time examining consumer-based XR endpoints, greater near-term impact is seen in the enterprise. This includes brands that use AR to promote products in greater dimension (B2B2C) and industrial enterprises that streamline their own operations (B2B).
These industrial endpoints include visual support in areas like assembly and maintenance. The idea is that AR’s line-of-sight orientation can guide front-line workers. Compared to the “mental mapping” they must do with 2D instructions, visual support makes them more effective.
And with VR, employee training and onboarding can be elevated through immersive sequences that boost experiential learning and memory recall. It also scales given that far-flung employees can get the same quality training, versus costly travel for senior training staff.
Altogether, there are micro and macro benefits to enterprise XR. The above micro efficiencies add up to worthwhile bottom-line impact when deployed at scale. Macro benefits include lessening job strain and closing the “skills gap,” which can preserve institutional knowledge.
But how is this materializing today and who’s realizing enterprise XR benefits? Our research arm ARtillery Intelligence tackled these questions in a recent report. It joins our report excerpt series, with the latest below on GE Healthcare’s immersive training program.
High-Stakes Outcomes
In Volume 2 of this series, we examined GE Healthcare’s AR-guided warehousing. Now we revisit the company for a different function: education and training. It wanted to evolve the way it trains and upskills technicians that service diagnostic equipment such as CT and MRI scanners.
Traditional training methods had drawbacks that could be improved given not only the need for operational efficiencies (as with all businesses), but high-stakes outcomes inherent in medical diagnostic equipment. The margin of error in these scenarios is human lives.
So it implemented an AR-based training program using Microsoft HoloLens 2*, Azure Remote Rendering, Spatial Anchors, and software from Adjacentech. This involved simulated models with step-by-step guidance with holographic vizualizations anchored to physical equipment.
This was meant to aid in memory retention through more dimensional and experiential learning – an effective principle when it comes to complex machinery. Beyond more effective training, these simulated environments mitigate the risk of costly equipment damage.
Immediate Impact
So what were the results? GE Healthcare was able to reduce training time per trainee by 4 hours. It also reduced the risk of equipment damage by $20 million. These gains were amplified by the fact that simulations could be tuned to emphasize the most common challenges for technicians.
As for strategic takeaways, one factor that stands out is that GE utilized AR as opposed to VR. The latter is often heralded for its strengths in training and immersive learning, because it can simulate processes in realistic ways. But AR can likewise be optimal in some situations.
In this case, Azure Remote Rendering and Spatial Anchors enabled realistic, multi-user, and dimensional training models. Additionally, AR’s value can be best realized in contexts where the stakes are high. As noted, GE Healthcare’s business has an immediate impact on human lives.
Areas where that statement applies tend to have a greater ROI from AR in that its impact transcends financial results (though that’s impactful too). This principle can be seen in fields such as aerospace & defense and commercial aviation as explored elsewhere in this report series.
*Though the lessons above sustain, Microsoft has retreated from the enterprise AR market to some degree, given HoloLens’ recent discontinuation.
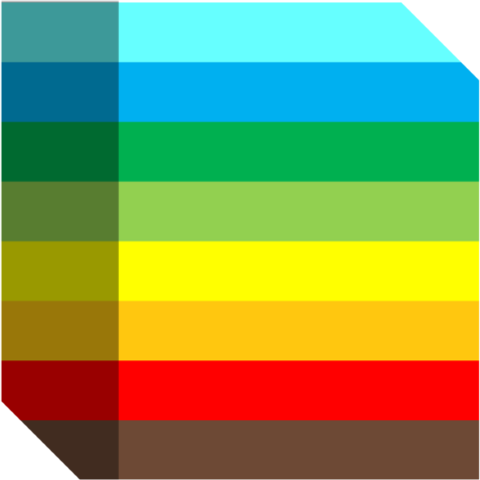