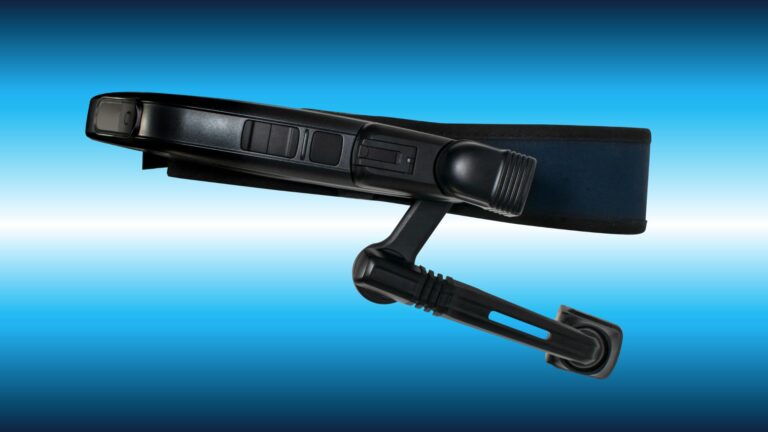
Though we spend ample time examining consumer-based XR endpoints, greater near-term impact is seen in the enterprise. This includes brands that use AR to promote products in greater dimension (B2B2C) and industrial enterprises that streamline their own operations (B2B).
These industrial endpoints include visual support in areas like assembly and maintenance. The idea is that AR’s line-of-sight orientation can guide front-line workers. Compared to the “mental mapping” they must do with 2D instructions, visual support makes them more effective.
And with VR, employee training and onboarding can be elevated through immersive sequences that boost experiential learning and memory recall. It also scales given that far-flung employees can get the same quality training, versus costly travel for senior training staff.
Altogether, there are micro and macro benefits to enterprise XR. The above micro efficiencies add up to worthwhile bottom-line impact when deployed at scale. Macro benefits include lessening job strain and closing the “skills gap,” which can preserve institutional knowledge.
But how is this materializing today and who’s realizing enterprise XR benefits? Our research arm ARtillery Intelligence tackled these questions in a recent report. It joins our report excerpt series, with the latest below on TÜV SÜD AR-guided work to safely de-commission nuclear plants.
Extra Set of Eyes
German safety, security, and sustainability firm TÜV SÜD is often tasked with lifecycle inspection and decommissioning nuclear power plants. Because of the level of danger inherent in these processes, the company was intent on finding ways to conduct its operations with greater safety.
Like many industrial enterprises, it is also constantly looking for ways to boost its operational efficiencies for its staff of 500+ experts and technicians. This led it to test and deploy RealWear’s assisted reality head-mounted tablet (HMT) to enable remote nuclear plant inspection.
HMT places a small flip-down microdisplay in the user’s line-of-sight to show information. In this case, Realwear’s hardware worked in tandem with Oculavis Share software to achieve remote expert support. Specifically, remote experts were paired with on-site inspectors wearing HMT-1.
This provided an extra set of expert eyes to monitor safe inspection practices. This importantly involved two-way communications where remote experts can see what the on-site tech sees and instruct in real time. Those instructions include voice as well as visual reference material.
Known Quantity
So what were the results? TÜV SÜD was able to deploy a lighter headcount to remote facilities – only one as opposed to the normally-required 2-3. This saved 11 hours of travel time and €4,000 in airfare per inspection. It could also cover more ground and achieve scalability in job volume.
As for strategic takeaways, Realwear demonstrated AR’s practicality over its novelty. In other words, it doesn’t have to be deeply immersive, a la Hololens 2, and the stuff of Hollywood movies. It’s often successful as a less-sexy, but realistic and pragmatic application of the technology.
As noted, Realwear does this by placing a flip-down microdisplay in the line-of-sight of front-line workers. This form factor makes its HMT flexible and accessible, often attached to a safety helmet. Furthering that end is the simplicity brought by the T in HMT… which stands for tablet.
Running on a customized version of Android, deployment and development occur through established channels. This sidesteps a point of friction often faced in enterprise AR: IT department resistance. Android, rather, is a trusted and known quantity to IT departments everywhere.
We’ll pause there and cue the full report. And stay tuned for more case study excerpts in the coming weeks…
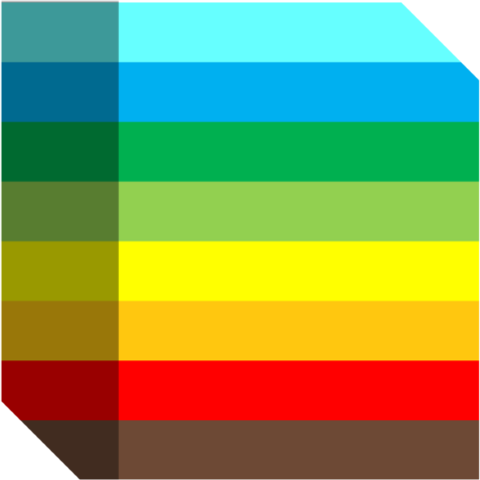