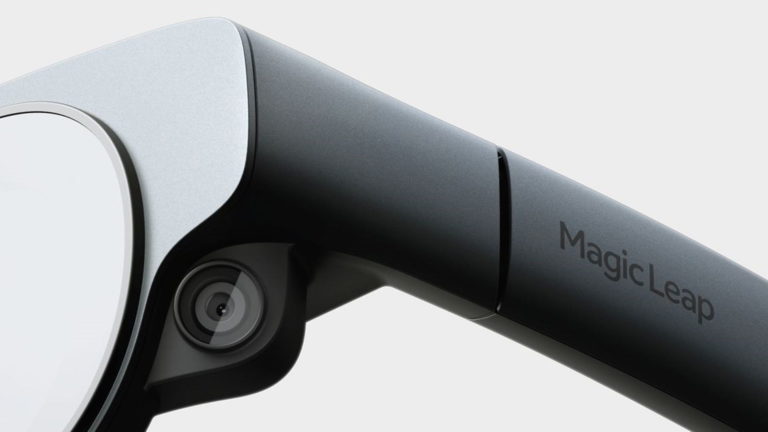
Though we spend ample time examining consumer-based XR endpoints, greater near-term impact is seen in the enterprise. This includes brands that use AR to promote products in greater dimension (B2B2C) and industrial enterprises that streamline their own operations (B2B).
These industrial endpoints include visual support in areas like assembly and maintenance. The idea is that AR’s line-of-sight orientation can guide front-line workers. Compared to the “mental mapping” they must do with 2D instructions, visual support makes them more effective.
And with VR, employee training and onboarding can be elevated through immersive sequences that boost experiential learning and memory recall. It also scales given that far-flung employees can get the same quality training, versus costly travel for senior training staff.
Altogether, there are micro and macro benefits to enterprise XR. The above micro efficiencies add up to worthwhile bottom-line impact when deployed at scale. Macro benefits include lessening job strain and closing the “skills gap,” which can preserve institutional knowledge.
But how is this materializing today and who’s realizing enterprise XR benefits? Our research arm ARtillery Intelligence tackled these questions in a recent report. It joins our report excerpt series, with the latest below on PBC Linear’s AR visual guidance to upskill technicians.
Institutional Knowledge
PBC Linear provides intelligent systems for manufacturing automation. Despite its operational acumen, it had an internal issue with new employee training in key functions like equipment maintenance. This was challenging, given the technical complexity of its systems.
Meanwhile, like many companies, it was losing senior-level skilled talent due to mass retirement among the outsized population of the baby boomer generation. This led to the dreaded “skills gap.” So it was motivated to more effectively disseminate valuable institutional knowledge.
Adopting a combination of Magic Leap 2 and Taqtile’s Manifest software, PBC Linear worked toward more effective distribution of knowledge and experience to novice front-line workers. To accomplish this, it created more than 100 templated AR sequences to guide complex processes.
This not only preserved, scaled, and placeshifted valuable institutional knowledge, but did so in a line-of-sight and hands-free way. This reduced the cognitive load that can impede accuracy and execution. This also worked towards reducing strain, and thus job satisfaction and morale.
Just-in-Time Knowledge
So what were the results? After getting the AR guidance sequences up and running in only six weeks, it was able to achieve a reduction in training time from 3 weeks to 3 days. It also saved $100,000+ per year on costs associated with redoing work and disposing of scrap materials.
As for top learnings and strategic takeaways, PBC Linear’s AR implementation demonstrates a key principle: guidance versus training. When done right, AR guidance can replace the need for training novice front-line personnel, while offering more effective and cost-efficient outcomes.
In other words, rather than spend time and resources getting novice personnel to learn everything they may encounter on the job, AR can deliver the right information at the right time – call it “just-in-time knowledge.” This should be considered as a key target for industrial enterprises.
Additionally, PBC Linear experienced a second-order effect: employee confidence. The technology empowered them, which has reportedly resulted in greater morale and retention – a key point given the generational skills gap noted earlier – as well as competitive recruiting efforts.
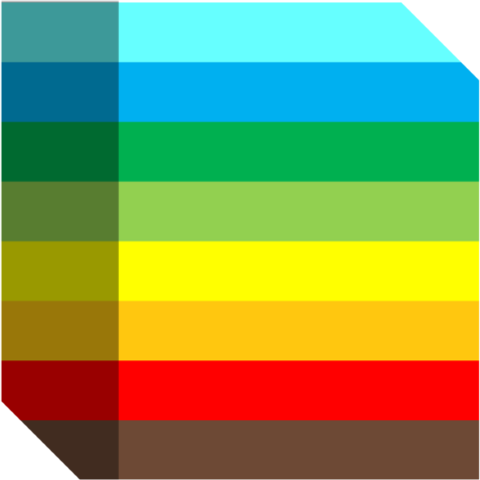